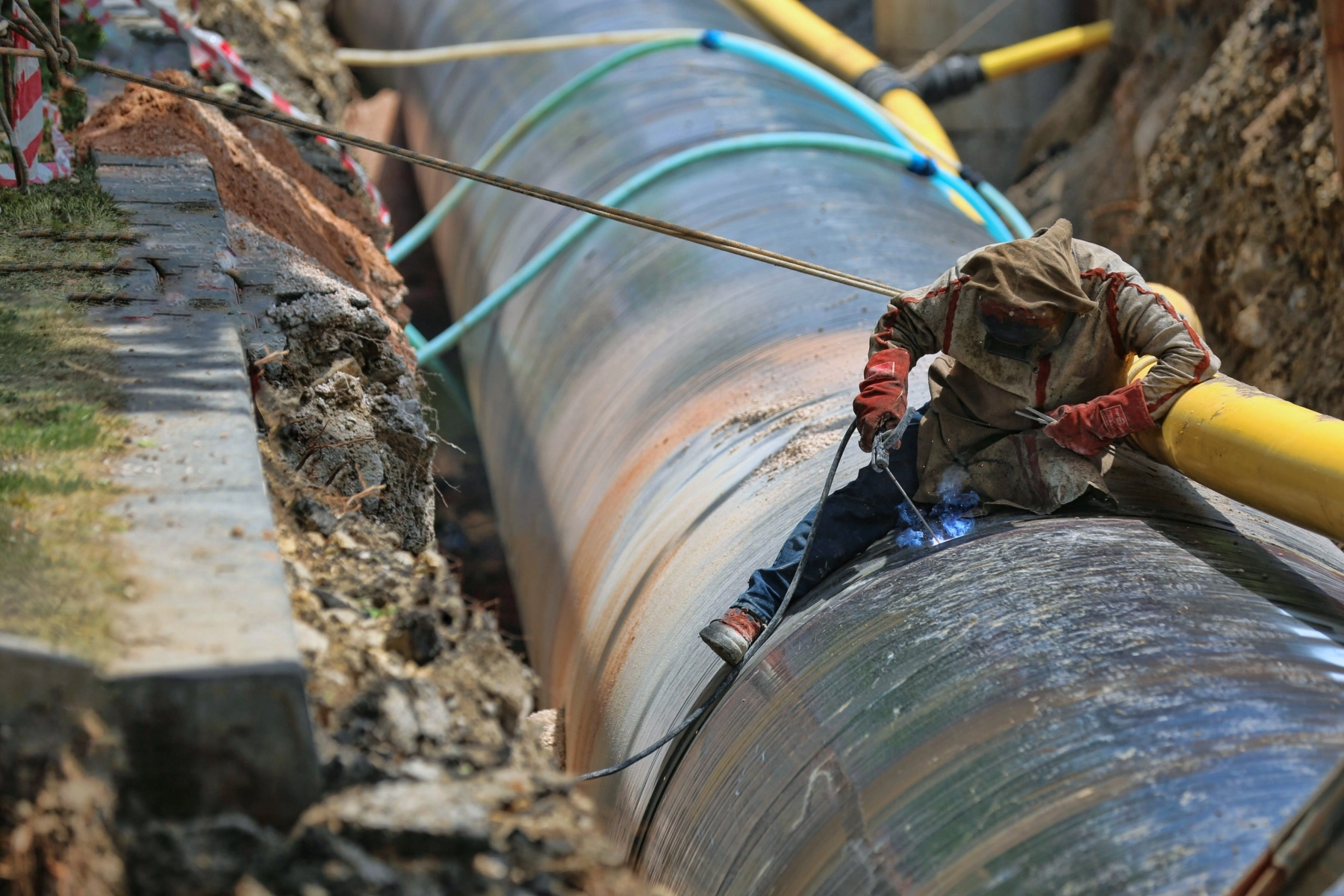
Advanced NDT solutions for comprehensive assessment
Pipelines serve as lifelines for industries worldwide, transporting fluids and gases critical for our daily lives. Ensuring the integrity of these pipelines is paramount, requiring advanced techniques to detect defects, assess damage depth, and control metal structures. Let's explore how innovative methods are revolutionising pipeline assessment across key areas of focus.
Defect search under the insulation layer without stripping
One of the greatest challenges in pipeline assessment is detecting defects hidden beneath insulation layers, without the need for costly and time-consuming stripping. Advanced NDT techniques, such as eddy-current testing and acoustic inspection, are paving the way for defect detection under insulation. Eddy-current probes can penetrate through insulation layers to detect surface defects, while acoustic sensors utilise sound waves to identify internal anomalies. These non-destructive methods enable inspectors to pinpoint defects accurately, ensuring comprehensive assessment without disrupting pipeline operations.
Damage depth assessment
Assessing the depth of damage within pipelines is essential for determining the severity of defects and implementing appropriate remediation measures. Crack depth meters, equipped with advanced sensing technologies, offer precise measurements of damage depth without compromising pipeline integrity. By evaluating the depth of cracks or corrosion, inspectors can assess the extent of structural damage and prioritise maintenance activities accordingly. This proactive approach to damage depth assessment helps mitigate risks and prolong the lifespan of critical pipeline infrastructure.
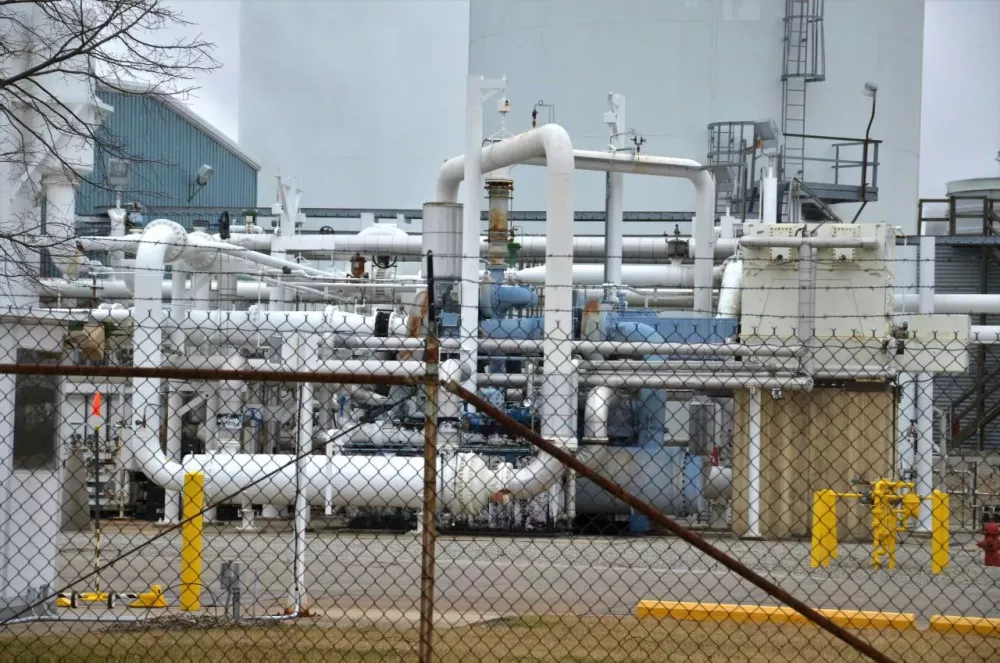
Control of metal structures
Metal structures within pipelines play a vital role in maintaining structural integrity and operational reliability. Implementing effective control measures is essential for preventing corrosion and ensuring long-term durability. and coating thickness gauges are indispensable tools for controlling metal structures and assessing their condition. By measuring material hardness and coating thickness, inspectors can evaluate the integrity of metal components and identify areas requiring maintenance or corrosion protection. This proactive approach to metal structure control helps minimise the risk of corrosion-related failures and ensures the continued safe operation of pipelines.
In conclusion, innovative techniques are transforming pipeline assessment practices, enabling comprehensive defect detection, damage depth assessment, and control of metal structures. By leveraging advanced NDT methods and precision instrumentation, inspectors can effectively safeguard critical pipeline infrastructure, mitigate risks, and ensure the reliable transportation of fluids and gases. Embracing these advancements in pipeline assessment is essential for maintaining operational safety, environmental stewardship, and industry sustainability in the years to come.
-
Portable hardness testers Commonly used in pipeline assessment to evaluate the hardness of metal components, particularly in areas prone to stress or corrosion. By measuring material hardness, inspectors can assess the integrity of pipeline materials and identify potential vulnerabilities such as material degradation or susceptibility to stress corrosion cracking. This information helps in determining the structural integrity of the pipeline and prioritising maintenance and repair efforts.
Flaw detectors: Play a critical role in detecting and characterising defects within pipeline structures. Eddy-current flaw detectors are frequently employed to detect surface cracks, corrosion, and other surface anomalies. Acoustic flaw detectors are utilised for detecting internal flaws such as laminations, delaminations, or voids within the pipeline material. Magnetic particle inspection (MPI) equipment is commonly used to detect and assess discontinuities in ferromagnetic materials, providing detailed insights into the condition of the pipeline.
Coating thickness gauges: Protective coatings are essential for preventing corrosion and extending the lifespan of pipelines. Coating thickness gauges are used to ensure the uniformity and integrity of protective coatings applied to pipeline surfaces. Inspectors measure the thickness of coatings to verify compliance with industry standards and identify areas that require maintenance or reapplication of protective coatings. This helps in preserving the structural integrity of the pipeline and minimising the risk of corrosion-related failures.
Crack depth meters: Utilised to evaluate the depth of cracks or fractures within pipeline structures. These meters provide accurate measurements of the depth of defects, allowing inspectors to assess the severity of structural damage and determine the appropriate course of action for repair or remediation. By evaluating crack depths, inspectors can prioritise maintenance activities and implement measures to mitigate the risk of failure in critical pipeline components.
Ferrite meters: Employed to assess the ferrite content in pipeline materials, particularly in stainless steel components susceptible to corrosion-induced cracking. By measuring the ferrite content accurately, inspectors can evaluate the material's susceptibility to corrosion and make informed decisions regarding material selection, welding procedures, and corrosion mitigation strategies. Ferrite meter readings enable proactive maintenance and ensure the long-term integrity of pipeline structures.
Overall, each of these instruments serves a specific purpose in pipeline assessment, ranging from evaluating material hardness and detecting defects to assessing coating integrity and measuring ferrite content. By utilising a combination of these instruments, inspectors can conduct thorough assessments of pipeline integrity, identify potential risks or vulnerabilities, and implement proactive maintenance strategies to ensure the safe and reliable operation of pipelines.