The Role of NDT equipment in the machine building sector
Addressing challenges in machine building inspections
The machine building sector, encompassing industries involved in the design, manufacture, and maintenance of machinery, faces numerous inspection challenges due to the complexity and precision required in component manufacturing.
From heavy industrial machinery and automotive parts to intricate mechanical assemblies and precision instruments, ensuring the quality and reliability of machine components is crucial for operational efficiency and safety
Critical inspection areas:
-
Heavy machinery: Components such as gearboxes, crankshafts, and large bearings in heavy machinery are subjected to significant operational stresses. These parts experience high loads and vibrations that can lead to wear, fatigue, and material failure. Detecting issues such as cracks, surface flaws, and hardness variations is essential to prevent unexpected breakdowns and ensure machinery performance.
-
Precision components: For precision machinery, such as those used in aerospace or medical devices, even minor defects can have severe consequences. Components like turbine blades, hydraulic pistons, and precision gears must meet stringent quality standards. Non-destructive testing (NDT) is crucial for detecting micro-cracks, inclusions, and dimensional inconsistencies that could impact performance.
-
Welds and joints: Welds and joints are critical areas in machinery construction, often subject to high stresses. The integrity of these welds is vital for overall machinery durability. Ensuring that welds are free from defects such as cracks, porosities, and incomplete fusion is essential for maintaining structural integrity and operational safety.
- Machinery assemblies: Complex assemblies often consist of multiple components that need to fit together precisely. Issues such as misalignment, incorrect assembly, or hidden defects can affect the functionality and longevity of the machinery. Regular inspection is necessary to identify potential issues before they lead to costly failures or performance issues.
Traditional inspection methods in machine building can be invasive, time-consuming, and sometimes disruptive to production schedules. For instance, dismantling complex machinery to inspect internal components can lead to extended downtime and increased costs. Moreover, the challenge of accessing tight spaces and intricate assemblies can complicate conventional inspection approaches.
TEQTO's solutions for machine building inspections
TEQTO provides a range of advanced non-destructive testing (NDT) equipment designed to tackle the unique challenges of the machine building sector effectively.
Metal hardness testers: Our metal hardness testers, utilizing Combined Testing Methods, UCI Testing Method, and Leeb Testing Method, are essential for assessing the hardness and strength of critical machine components. Accurate hardness measurements ensure that parts like gearboxes and crankshafts can withstand operational stresses without premature wear or failure.
Magnetic particle flaw detectors: Ideal for detecting surface and near-surface defects in ferromagnetic materials, our magnetic particle flaw detectors are perfect for inspecting welds, gear teeth, and structural components. By revealing hidden flaws such as cracks and porosities, these detectors help maintain the integrity and reliability of essential machinery parts.
Eddy-current flaw detectors: Using electromagnetic induction, our eddy-current flaw detectors excel in identifying surface defects and material inconsistencies without direct contact. This is particularly useful for inspecting precision components, such as turbine blades and hydraulic pistons, ensuring that they meet stringent quality standards.
Acoustic flaw detectors: High-frequency sound waves used in our acoustic flaw detectors provide detailed insights into the internal condition of machine components. This method is crucial for detecting internal defects in complex assemblies and precision parts, offering a non-invasive way to ensure their structural integrity and functionality.
Coating thickness gauges: Our coating thickness gauges measure the depth and uniformity of protective coatings applied to machinery parts. Ensuring that coatings meet specifications helps prevent corrosion and wear, maintaining the longevity and performance of components such as hydraulic cylinders and gear assemblies.
Ferrite meters: Accurate measurement of ferrite content in stainless steel welds helps assess the corrosion resistance and mechanical properties of welds in critical machine components. TEQTO’s ferrite meters provide the necessary data to ensure that welds are within acceptable limits, enhancing the durability of key machinery parts.
Crack depth meters: Measuring the depth and orientation of surface cracks, our crack depth meters are essential for evaluating damage in components such as crankshafts and gearboxes. Precise crack depth measurements help plan repairs and prevent failures, ensuring that machinery operates smoothly and reliably.
By incorporating TEQTO’s advanced NDT tools into your machine building processes, you can effectively address the sector's unique inspection challenges. Our equipment enhances safety, efficiency, and reliability, helping to prevent failures and extend the lifespan of critical machinery components in a highly demanding industry.
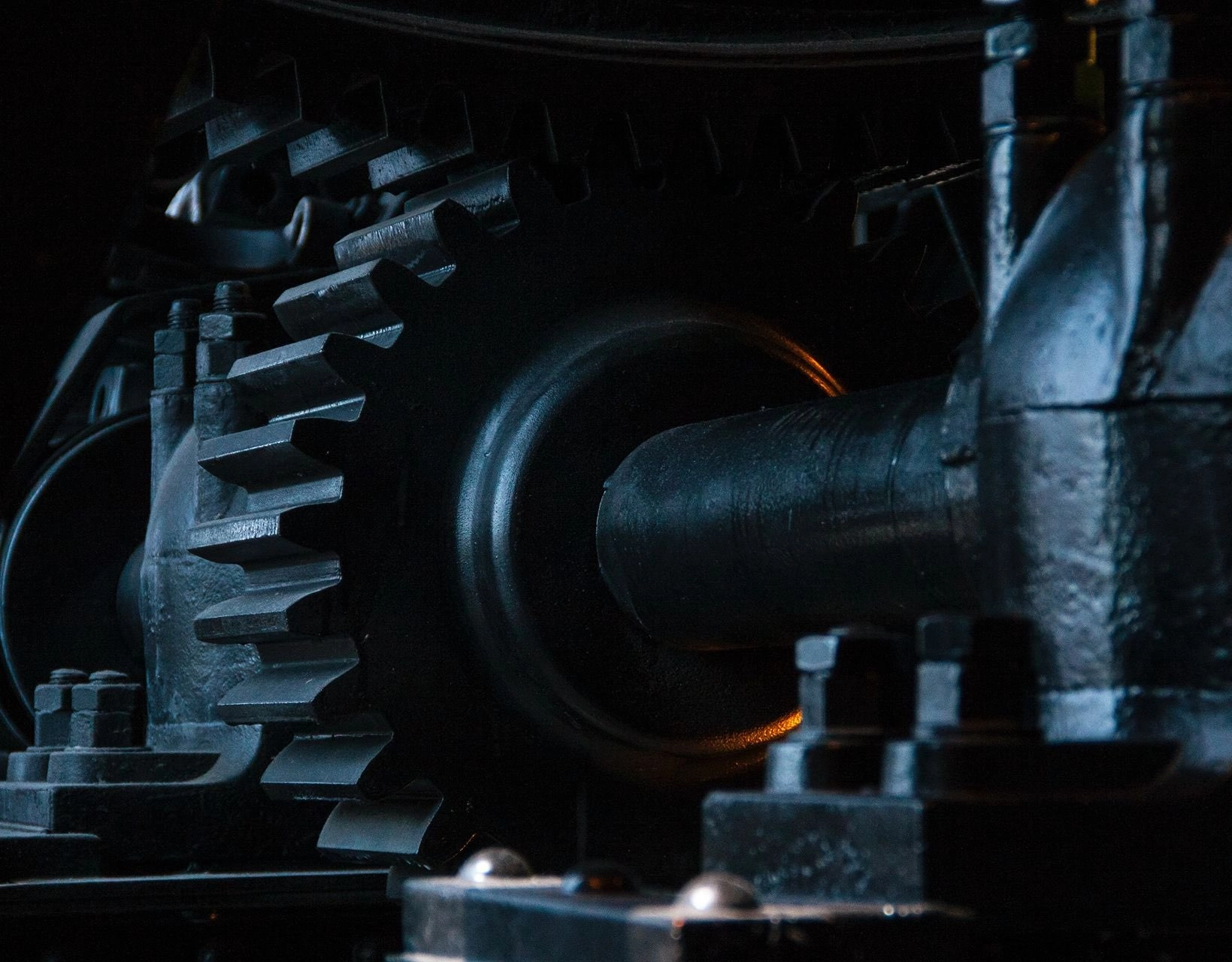