The Role of NDT equipment in the power generation sector
Tackling inspection challenges in power generation
The power generation sector, encompassing utilities, renewable energy facilities, and industrial power plants, faces a range of complex inspection challenges due to the critical nature of its infrastructure. Ensuring the reliability and safety of power generation equipment is vital to maintaining continuous operations and avoiding costly downtime.
Components in this sector, including turbines, generators, boilers, and pipelines, are subjected to extreme conditions that can lead to material degradation and equipment failure.
Critical inspection areas:
-
Turbines and generators: Turbines and generators operate under high stress and temperature conditions, making them susceptible to wear, fatigue, and material failure. Detecting issues such as cracks, corrosion, and wear in turbine blades and generator components is crucial to preventing operational interruptions and ensuring efficient power generation.
-
Boilers and heat exchangers: Boilers and heat exchangers are essential for efficient energy transfer and heat management in power plants. The integrity of these components is vital to preventing leaks, corrosion, and structural failures. Non-destructive testing (NDT) helps identify flaws such as weld defects, erosion, and material thinning before they compromise system safety and efficiency.
-
Pipelines and pressure vessels: Pipelines and pressure vessels transport fluids and gases at high pressures, making their integrity critical for safe operations. Regular inspection is needed to detect issues like corrosion, cracking, and weld defects that could lead to leaks or explosions. Ensuring these components meet safety standards is essential for preventing environmental and safety hazards.
-
Electrical insulation: Insulation materials in electrical components such as transformers and circuit breakers can degrade over time due to thermal and electrical stresses. Inspecting these materials for signs of deterioration or breakdown is crucial for maintaining electrical safety and system reliability.
Traditional inspection methods in power generation can be invasive and disruptive, often requiring shutdowns or partial dismantling of equipment. For instance, inspecting internal boiler tubes or turbine blades typically involves significant downtime and labor. Moreover, the challenge of accessing critical areas for inspection can complicate conventional methods, increasing costs and operational disruptions.
TEQTO's solutions for power generation inspections
TEQTO offers a suite of advanced non-destructive testing (NDT) equipment tailored to address the specific inspection needs of the power generation sector.
Metal hardness testers: Our metal hardness testers, featuring Combined Testing Methods, UCI Testing Method, and Leeb Testing Method, are vital for assessing the hardness and strength of critical components such as turbine blades and pressure vessel materials. Accurate hardness measurements ensure these parts can withstand the high operational stresses they encounter.
Magnetic particle flaw detectors: Designed to detect surface and near-surface defects in ferromagnetic materials, our magnetic particle flaw detectors are essential for inspecting welds and structural components in boilers, turbines, and pressure vessels. These detectors help reveal hidden flaws like cracks and porosities, maintaining the structural integrity of crucial power generation equipment.
Eddy-current flaw detectors: Utilizing electromagnetic induction, our eddy-current flaw detectors are excellent for identifying surface defects and material inconsistencies in conductive components. This is particularly useful for inspecting turbine blades and generator parts, ensuring they meet rigorous quality standards.
Acoustic flaw detectors: High-frequency sound waves used in our acoustic flaw detectors provide detailed insights into the internal condition of power generation components. This method is effective for detecting internal defects in boilers and heat exchangers, offering a non-invasive way to ensure their structural integrity.
Coating thickness gauges: Our coating thickness gauges measure the depth and uniformity of protective coatings on equipment such as pipelines and electrical insulation. Ensuring coatings meet specifications helps prevent corrosion and wear, maintaining the performance and safety of critical components.
Ferrite meters: Measuring ferrite content in stainless steel welds helps assess the corrosion resistance and mechanical properties of welds in components like heat exchangers and pressure vessels. TEQTO’s ferrite meters provide essential data to ensure welds meet safety and performance standards.
Crack depth meters: Our crack depth meters are crucial for measuring the depth and orientation of surface cracks in power generation components such as turbine blades and pressure vessel materials. Accurate crack depth measurements assist in planning repairs and preventing failures, ensuring reliable and safe power generation.
By integrating TEQTO’s advanced NDT tools into your power generation maintenance routines, you can effectively manage the sector's inspection challenges. Our equipment enhances safety, efficiency, and reliability, helping to prevent failures and extend the lifespan of critical power generation infrastructure.
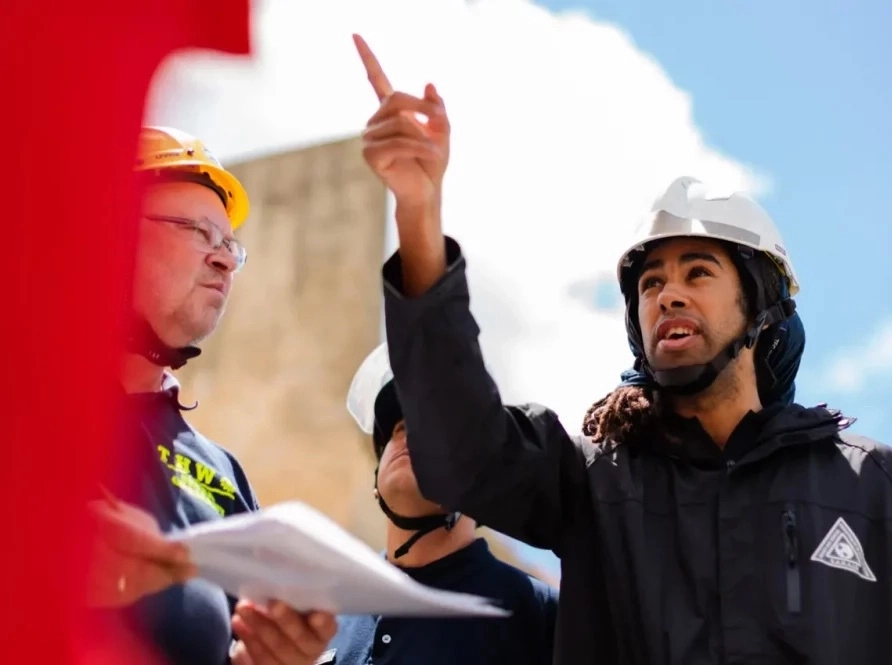