Claus Kleesattel's invention, the Ultrasonic Contact Impedance (UCI) method, has been employed in the metal-processing industry for over half a century.
The UCI hardness testing method is a non-destructive testing technique that uses ultrasonic contact impedance to measure the hardness of materials. It is particularly useful for testing metals and alloys, as it provides accurate and reliable results without damaging the test specimen. The UCI method is based on the principle that the frequency shift of an ultrasonic wave is proportional to the indentation size produced by a Vickers diamond indenter. This relationship allows for the determination of the Vickers hardness value, which is a measure of a material's resistance to penetration under a specific load.
Principles of UCI Hardness Testing
The UCI hardness testing method works by exciting a metal rod with a Vickers diamond indenter attached to its end into longitudinal oscillation at a frequency of approximately 70 kHz using piezoelectric transducers. When a test load is applied, a frequency shift occurs as the diamond penetrates into the material, with the frequency shift being greater for larger indentations and smaller for harder materials. The frequency shift is proportional to the size of the indentation produced by the Vickers diamond, which is described by equation:
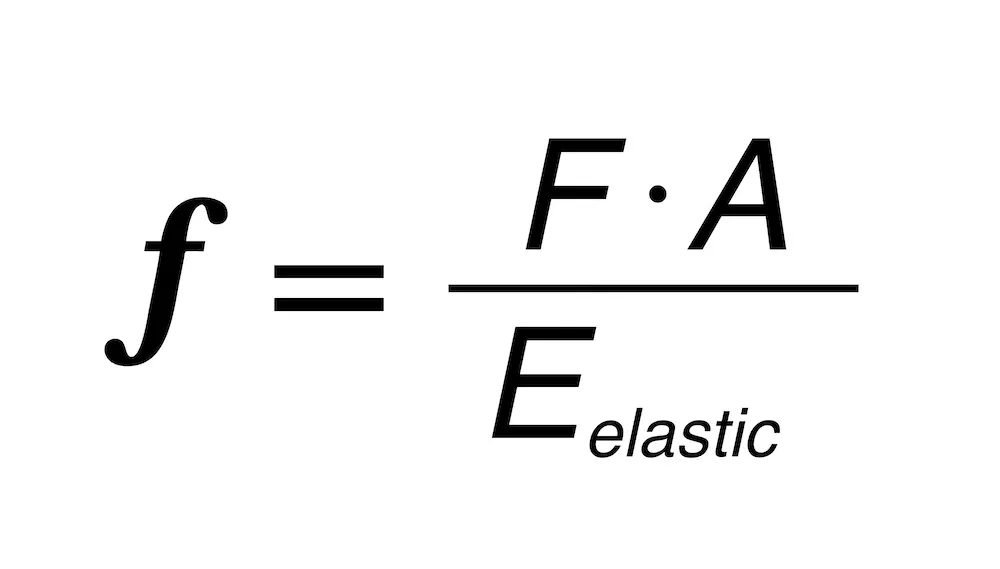
The frequency shift (f) is proportional to the area of indentation (A) generated by the Vickers diamond, the force applied in the test (F), and the Young's Modulus of the material (E elastic).
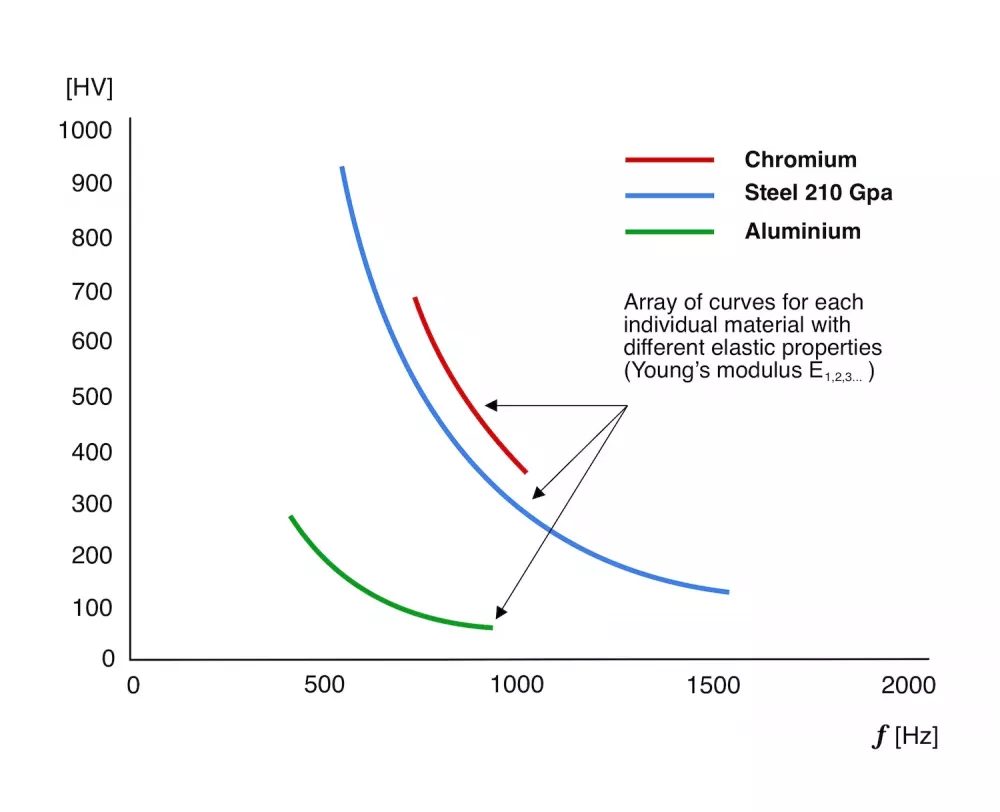
Variations in Young's modulus among materials lead to distinct sets of curves. It's noteworthy that certain steel alloys, like Cr-Mn steels, belong to the same material class due to their consistent Young's modulus. However, materials such as austenitic stainless steels, duplex steels, or Inconel may necessitate individual calibration against an appropriate reference. Furthermore, adjustments may also need to account for surface roughness. Thus, maintaining similarity in material processing is crucial.
Advantages of using portable equipment for UCI hardness testing
Portable hardness testing equipment, such as those using the UCI (Ultrasonic Contact Impedance) method, offers several advantages over traditional benchtop hardness testers:
1. On-site assessment: Portable devices allow for in-situ hardness measurements, which can be particularly useful for inspecting components that cannot be moved or are difficult to access, complex geometries such as gears and pipe bends.
2. Flexibility: Portable equipment allows for measurements in difficult-to-reach locations and during the production, manufacturing, or assembly process, as it is not limited to the vertical position like conventional stationary hardness testing machines
3. Quick and economical: Portable UCI hardness testers can perform the test procedure relatively quickly, making them suitable for use in production environments and maintenance tasks.
4. Non-destructive: Unlike traditional hardness testing methods, such as Rockwell, Brinell, or Vickers tests, which require the test piece to be brought to the testing device, UCI hardness testing is non-destructive, as it does not require the removal of material from the test specimen.
5. Accuracy: The UCI method provides accurate hardness measurements, especially on fine-grain, homogeneous materials that are of sufficient mass and thickness to negate the effects of sympathetic oscillations and flexural waves produced by probe tip vibrations.
6. Versatility: The UCI method is suitable for testing small parts, thin-walled products, components with difficult access to the testing area, and surface-hardened layers.
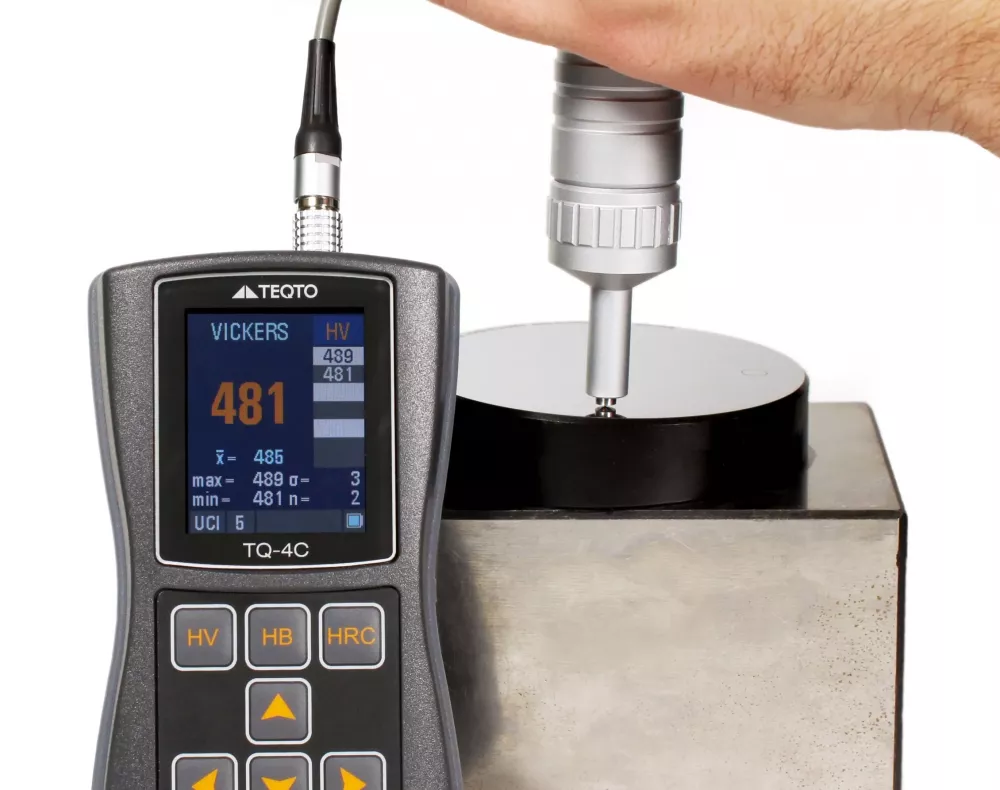
UCI hardness testing using TEQTO’s TQ-4C series
Application of the UCI method
The UCI hardness testing method, based on ultrasonic contact impedance, finds applications in various industries due to its portability, speed, and reliability. Some extended applications of the UCI method include:
1. Incoming goods inspection: UCI hardness testing is suitable for inspecting incoming goods to ensure they meet the required hardness specifications.
2. Mix-up checks: The method can be used to verify the hardness of components to prevent mix-ups in manufacturing processes.
3. Heat-affected zone (HAZ) testing: UCI is valuable for testing the heat-affected zone of welds, providing insights into the hardness changes in these critical areas.
4. Testing of difficult-to-reach areas: UCI is effective for testing areas that are challenging to access, such as gear teeth, bearings, and other confined spaces.
5. Automated applications: Due to its simplicity and speed, UCI is a preferred solution for automated hardness testing applications, enhancing efficiency in production environments.
6. Surface processing inspection: UCI can be used to assess the hardness of components after surface treatments to ensure the desired hardness properties are achieved.
7. Weld inspection: The method is suitable for inspecting welds to verify the hardness of the welded joints, ensuring structural integrity.
8. Coat hardness measurement: UCI can be utilised to measure the hardness of coatings, such as those on gravure cylinders, providing crucial information on coating quality and durability.
Types of materials
The UCI (Ultrasonic Contact Impedance) method is versatile and suitable for testing various types of materials. According to the provided sources, the UCI method can be used to test the hardness of:
1. Fine-grained materials of any shape and size, especially where material properties need to be processed with narrow tolerances, such as for determining strain hardening on drop forged parts.
2. Small parts, thin-walled products, and components with difficult access to the testing area, including surface-hardened layers.
3. Serial parts after heat treatment, after surface processing, welds, and coat hardness measuring on gravure cylinders.
4. Materials with different values of Young's modulus, as the frequency shift in the UCI method depends on this material constant.
5. Components where classic hardness testing methods like Vickers, Rockwell, or Brinell are not practical or possible, such as in incoming goods inspection, production control, or maintenance on integrated components.
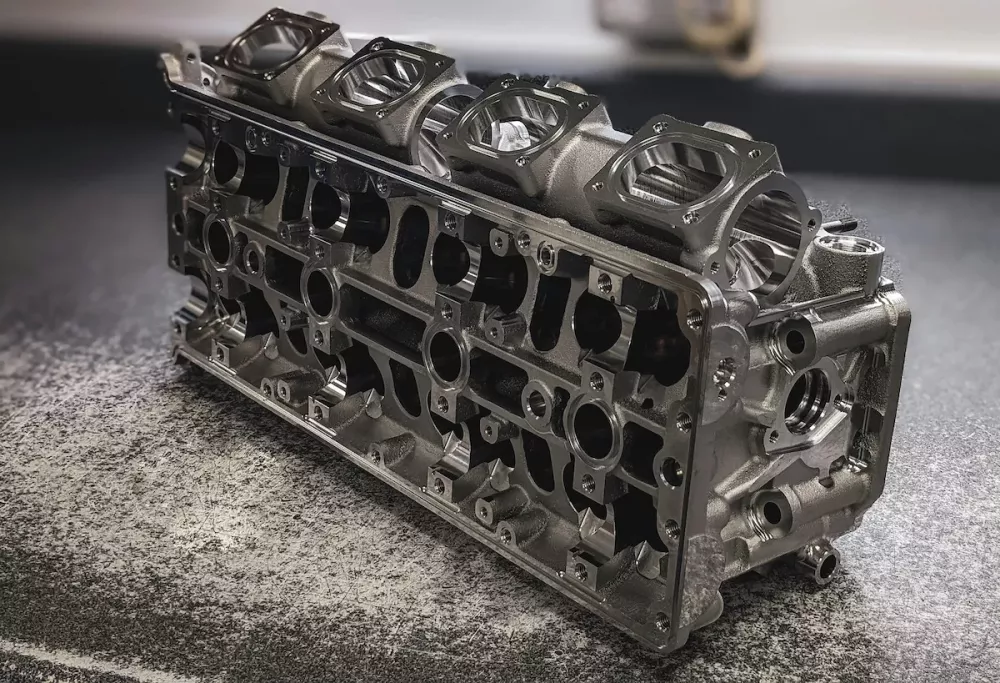
Industries
Some extended industries where the UCI method is commonly used include:
1. Aerospace: In the aerospace industry, the UCI method is used to test the hardness of critical components like turbine blades, landing gear, and structural elements to ensure their integrity and durability under extreme conditions.
2. Automotive: Automotive manufacturers use the UCI method to assess the hardness of engine components, gears, shafts, and other parts subjected to high stress and wear, ensuring quality and performance.
3. Manufacturing: The UCI method is valuable in manufacturing industries for testing the hardness of machined parts, tools, dies, and moulds to maintain quality standards and optimise production processes.
4. Oil and gas: In the oil and gas sector, the UCI method is employed to evaluate the hardness of pipelines, valves, and drilling equipment to prevent failures and ensure safety in harsh operating environments.
5. Medical devices: The UCI method is applied in the medical device industry to test the hardness of implants, surgical instruments, and medical equipment to meet regulatory requirements and ensure patient safety.
6. Electronics: Electronics manufacturers use the UCI method to assess the hardness of components like circuit boards, connectors, and housings to guarantee reliability and longevity of electronic devices.
7. Mining: In the mining industry, the UCI method is used to test the hardness of materials used in mining equipment, tools, and infrastructure to withstand abrasive and high-impact conditions.
8. Construction: The UCI method finds applications in the construction industry for testing the hardness of structural steel, concrete, and building materials to ensure compliance with safety and quality standards.
9. Railway: Railway companies utilise the UCI method to assess the hardness of rail tracks, wheels, and components to maintain operational efficiency and safety in rail transportation systems.
10. Marine: In the marine industry, the UCI method is employed to test the hardness of ship components, propellers, and marine structures to withstand corrosion and harsh marine environments.
11. Power generation: Hardness testing is crucial for assessing the integrity and residual life of in-service components in power generation equipment, such as gas turbines, steam turbines, and generators.
12. Metalworking: Portable UCI hardness testers are used in the metalworking industry to measure the hardness of screws, bolts, and other components.
13. Maintenance and production: Portable UCI hardness testers are used in maintenance tasks and production control to ensure the quality and durability of components.
Limitations
While UCI hardness testing offers many advantages, there are some limitations to consider:
1. User-dependent: The accuracy of UCI hardness testing can be influenced by the skill and experience of the operator, as the method may become more user-dependent if the test is not performed in a steady location orthogonal to the test surface.
2. Indentation size: The method may be less accurate for tiny indentations, as even a slight probe movement during the test can significantly impact the reading.
3. Calibration: Proper calibration is required to ensure the accuracy of the test results, and calibration samples with known hardness values should be used to achieve accurate results for specific materials.
4. Best suited for homogeneous materials: The UCI method is best suited for materials having a homogeneous microstructure. The small size of the sampled area is unable to provide consistent and dependable results on most cast and forged materials
In conclusion, the UCI hardness testing method using portable equipment offers a non-destructive and quick solution for measuring the hardness of metals and alloys in various industries. While there are limitations to consider, the advantages of on-site assessment and the ability to test in-situ make UCI hardness testing a valuable tool for maintaining the integrity and durability of components in power generation, metalworking, and other industries.
TEQTO’s answer to portable UCI hardness testing: TQ-4C series
The TQ-4C is a high-precision handheld instrument designed for demanding production and field conditions. Operating on the Ultrasonic Contact Impedance (UCI) method, this tester is specifically tailored for measuring the hardness of carbon construction steels across fundamental hardness scales such as Brinell (HB), Rockwell (HRC), and Vickers (HV). It is suitable for a wide range of materials, including heat-proof, corrosion-proof, and non-corrosive steels, as well as plated coatings and items with complicated configurations.
The TQ-4Combi is a high-precision handheld instrument equipped with brand-new software, designed for non-destructive testing of production quality. It combines the advantages of both UCI and Leeb methods for precise control of metals and alloys hardness. Suitable for a wide range of applications, including carbon and structural steels, hard-surfaced items, heat-resistant and corrosion-resistant steels, non-ferrous metals and alloys, electroplated coatings, items of complex configuration, thin-walled and small-sized items, and large items and heavy-duty equipment.